Steel mill blasts away lighting maintenance worries with LED conversion
When you operate a rough-and-tough steel mill where the furnaces hit 2300°F, where hydrochloric acid washes impurities from finished metal, where industrial rollers crank and churn as they flatten slabs down from 10 inches to 1-inch sheets and smaller, where welders' arcs flare in the maintenance room and workers fight dust and dirt everywhere, the last thing you want to worry about is replacing lightbulbs.
Interested in articles & announcements on indoor/outdoor industrial LED lighting?
Yet that's what they were doing at the 350-acre NLMK steel works in Farrell, PA, about 70 miles northwest of Pittsburgh, both inside the cavernous halls and outside on the roads, the parking lots, and at the pumping station along the Shenango River.
"I had people in bucket trucks going around pretty much almost every day of the week, pretty much they were going around replacing bulbs and ballasts - I had to keep one guy on street lighting all year long," recalled NLMK corporate risk manager Jeff Stidham. Yet, all the while, "we had a steel mill we were trying to run," he added.
Or as senior plant electrical engineer Mike Allenbaugh put it, "We are lightly staffed on our maintenance, and we don't want to be working on our lights all the time." He recalled that high-bay metal-halide (MH) lamps would frequently dim out so that "probably about once a year we had to have somebody go up and change bulbs on them." With ceiling heights around 60 ft in some locations, replacement was never easy.
That was in NLMK's not-too-distant past, which included the MH high bays as well as fluorescents, sodium-vapor lamps, and other light sources for street lamps, area lighting, and other functions. The mill had around 10,000 of the older-technology lamps as recently as 2012. It had been considering installing LED lighting for several years prior to that, tempted in large measure by the promise of longer lifetimes and, eventually, 10-year warranties from British industrial LED lighting vendor Dialight.
"Once every year-and-a-half to two years with conventional lighting, they were needing to change out lamps - relamp the facility or swap out whole entire fixtures," said Dialight regional sales manager Ryan Antonikas. "Any time you do that in a heavy industrial location, whether it's a steel mill or not, it's pretty costly to do so. You have a lot of safety concerns, you have to shut down equipment, lock out, tag out, make a lot of safety precautions just to change a lamp or a ballast."
NLMK had evaluated LED lighting as early as 2008, but the solid-state lighting (SSL) simply wasn't ready. For one reason, it didn't emit enough lumens to provide adequate illumination, which was of particular concern for high-bay installations at the works.
"LEDs just weren't that good back then," said Allenbaugh. "They were very expensive and they weren't as bright as the fluorescents."
But by 2010, SSL technology from Dialight was beginning to improve to the point where NLMK believed it could start to meet the needs of its heavy-duty environment.
">Hot News
Recommended Products
HT-30J HaoTian 30-liter Stainless Steel Silent Wet and Dry Vacuum Cleaner
Inquiry Guangzhou Haotian Cleaning Equipment Technology Co., Ltd.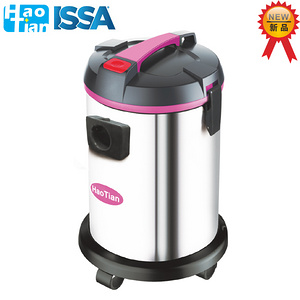
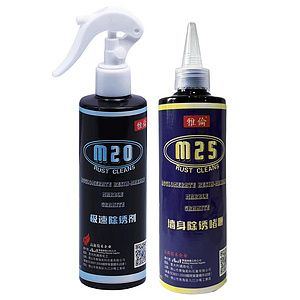
LC80-3 LICHI 80L Three-motor stainless steel wet and dry vacuum cleaner(tilt)
Inquiry Guangzhou Haotian Cleaning Equipment Technology Co., Ltd.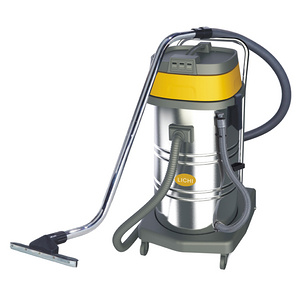
LC60-3 LICHI 60L Three-motor stainless steel wet and dry vacuum cleaner
Inquiry Guangzhou Haotian Cleaning Equipment Technology Co., Ltd.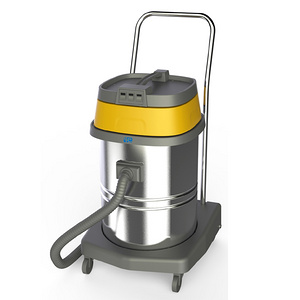
SVAVO Center Pull Toilet Paper Dispenser PL-151066
Inquiry SHENZHEN SVAVO INTELLIGENT TECHNOLOGY CO.,LTD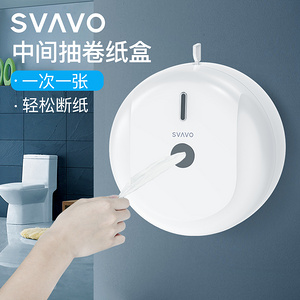
SVAVO Center-Pull Toilet Paper Dispenser ZM-066
Inquiry SHENZHEN SVAVO INTELLIGENT TECHNOLOGY CO.,LTD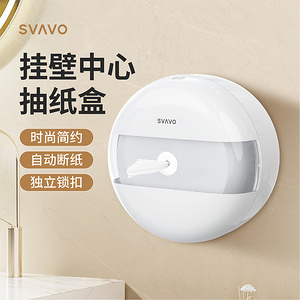
SVAVO Dual Center-Pull Toilet Paper Dispenser ZM-066D
Inquiry SHENZHEN SVAVO INTELLIGENT TECHNOLOGY CO.,LTD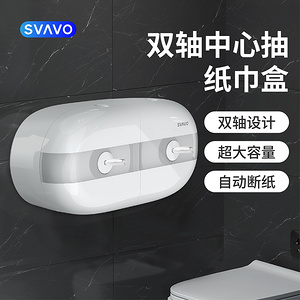
HT-10S HaoTian 10-liter Plastic Silent Dry Vacuum Cleaner
Inquiry Guangzhou Haotian Cleaning Equipment Technology Co., Ltd.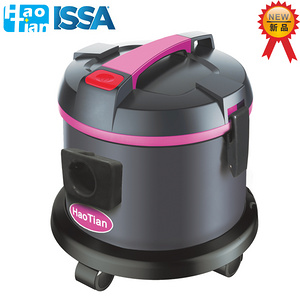