Cross-laminated timber (CLT) is becoming increasingly common in wooden structures being used as pre-fabricated wall and floor elements. CLT products are normally made of several wooden layers, stacked on top of each other, glued together and arranged so that the wood fibres of each layer are perpendicular to those of the neighbouring layers. The layers themselves consist of boards that are edge-glued together.
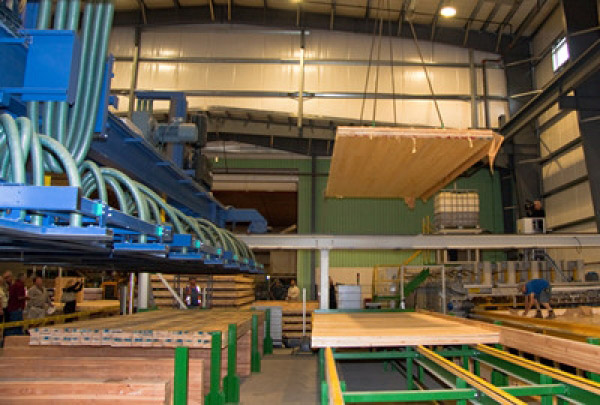
Usually, an odd number of layers are used. This results in a product with high dimensional stability and load bearing capabilities in more directions than regular sawn timber or glulam. In most cases, sawing small diameter logs results in lower volume yield than sawing large diameter logs. This is due to the geometry of logs; fitting rectangular blocks inside an approximately cylindrical shape, ie:boards into logs is more difficult for small diameters of the cylinders than for large diameters.
If logs could be sawn in a way that follows the outer shape of the log to a larger degree, yield could be increased, especially for small diameter logs. Small diameter logs are defined as logs with a top diameter of less than 185 mm. When processing logs of this size, the volume yield is often below 45 percent. All other logs were considered as ‘large’ within this context.
The hypothesis of the study was that following the shape of the log when sawing can be done in the edging operations of a sawmill, where boards are sawn into trapeze shapes instead of rectangular blocks. These trapeze shapes can then be glued together to form a rectangular end product, in order to take care of the trapeze-shaped pieces in a proper way.
In this case, a CLT product is suitable since it is normally made out of several edge glued wood pieces. The objective of the study was to investigate how much yield can be improved by using an edging method called trapeze edging, which follows the natural taper of boards, compared to a normal straight edging method, for production of boards for CLT panels.
This was tested both for logs of varying size, as well as for small diameter logs, through sawing simulation. The study was based on 4,860 logs: 1465 computed tomography (CT) scanned logs from the Swedish Stem Bank (SSB), and 3,395 logs that were scanned at a Swedish sawmill using a RemaLog optical 3D scanner. The wood species distribution was 48.3 percent Norway spruce and 51.7 percent Scots pine.
In general, sawn timber from spruce has a modulus of elasticity of around 8 to 15 GPa, a dry density of roughly 300 to 500 kg/cubic metre, and a bending strength of around 30 to 60 MPa. For pine, the material properties are rather similar, with a modulus of elasticity of around 8 to 12 GPa, a dry density of about 300 to 500 kg/cubic metere, and a bending strength of 30 to 45 MPa.
These properties vary between specimens and depend on other factors than the wood species alone. For individual boards, the properties can be far smaller or greater than the intervals stated. The outer shape of the SSB logs was obtained from CT scanning data. It was described at 10 mm-intervals in the lengthwise direction of the log, as a radius at each degree for all 360 degrees of the log cross section, measured from the pith to the log surface.
For the logs scanned at the sawmill, the outer shape was described at 100 mm intervals, and a cross section radius at every tenth degree. These outer shape descriptions were the basis for sawing simulations, and were also used to calculate the volume of each log.
Sawing simulation Scanned logs, such as those of the Swedish Stem Bank, can be used for sawing simulation through the simulation software Saw2003, developed by Nordmark. The input is log models, based on scanning of logs, either by a 3D optical scanner or a CT scanner.
The software models a sawmill that employs cant sawing with two sawing machines, with curve sawing in the second saw. When edging and trimming is performed in the software, the results are virtual boards with information about dimensions, value, quality, and so on. If edging and trimming is not performed, then the results are shape profiles of un-edged board flitches
The study was made using four scenarios. Two reference scenarios are based on cant sawing of logs, a common procedure in many sawmills. The two CLT product scenarios are based on trapeze edging and production of CLT panel layers. One reference and one CLT scenario had all logs as input data, while the two others had only logs with a top diameter of less than 185 mm as input data.
This limit was set to separate between small diameter and large diameter logs, and correspond to the separation of the fourth and fifth sawing pattern.
Two reference scenarios, 1 and 2, were tested. In reference scenario 1 all logs were used, and in reference scenario 2 logs of a top diameter of less than 185 mm were used. The number of logs in the latter group was 2, 214. In these scenarios, all logs were sawn in the program using a cant sawing pattern, that was decided for each log depending on top diameter.
This represents the regular production procedure of many sawmills. Sideboards were edged, and all boards were trimmed to the Nordic Timber Grading Rules grade B. Only wane was considered since internal defects of the logs were not used. After edging and trimming the dried and planed dimensions of all boards were calculated. This was used to calculate the yield of the two scenarios, as total produced dried and planed board volume divided by total log volume.
In two alternative scenarios, called A and B, sawn timber resulting from s awing simulation was further processed into a CLT product. The product used as target in this study was a wall element used for pre-fabrication of houses. It was made from three timber layers, 16,000 × 2,450 mm, with a thickness of 20, 30, or 40 mm, stacked on each other and glued together. No wane was allowed in the pieces used for CLT production.
Two types of layers were used in the CLT products, L-layers and C-layers. The L-layers had lengthwiseoriented boards, ie: 16 m long finger-jointed boards glued together to 2.45 m width, while the C-layers had crosswise oriented boards, ie: 2.45 m long boards glued together to 16 m width.
The largest difference between the reference scenarios and the alternative scenarios was that a trapeze edging method was employed rather than a straight edging method for board flitches. Trapeze edging was done by following the natural taper of the sawn surface of a flitch. The direction of the two edges was decided in three steps for each side, left and right.
First, a linear regression line was fitted to the edge of the sawn surface. Secondly, the regression line was moved vertically until it tangent a single point of the wane. Thirdly, the line was tilted counter-clockwise or clockwise, until it encompassed another point of the wane. The tilting direction resulting in the largest total volume of the edged board was chosen. Consequently, the shape of the trapeze edged piece depends on the shape of the sawn flitch.
The shape profile description of each sideboard flitch resulting from sawing simulation was exported to a data file, and further processing of these flitches was modelled in a program specifically written for this purpose.
The following operations were done on the profile data: Each sideboard flitch was crosscut at a position 250 cm from the butt end. This corresponded to the CLT panel width plus a five cm margin for crosscutting errors, end cracks and so on. The result of this was a butt end flitch and a top end flitch. The 250 cm long butt end flitch was edged using trapeze edging, while the top end flitch was straight edged, maximizing the volume of the obtained board. The straight edging was done in 10 mm modules, starting at 30 mm.
A minimum allowed length was set at 1.5 times the board width, or 200 mm, whichever was smallest. Apart from this the length was set to the one giving the highest possible yield. The trapeze edged pieces were used for C-layers, while the straight edged pieces were finger-jointed, crosscut at 16 m length, and stacked to be used as L-layers.
To form C-layers, trapeze edged boards was stacked together edge to edge until the target length of 16 m was acquired. Stacking the trapezoidal pieces In order to make layers of the trapeze edged pieces without the sheet wheeling out of control, stacking was done using a method where each trapeze edged piece could beplaced in either direction.
The direction chosen was the one resulting in the smallest angle of the upper edge of the CLT layer, ie: keeping the sheet as straight as possible at all times by alternating how the next piece is placed. All pieces were pushed as far as possible to one side to avoid aggregating errors. The edge unevenness was less than two mm when using this strategy.
This CLT scenario was based on the same sawing patterns as in the reference scenarios, ie:cant sawing patterns. In this scenario all 4,860 logs were used. The centre boards resulting from sawing simulation were trimmed and planed to be used as regular sawn timber. The side boards were sawn at 24 mm green thickness which corresponded to a nominal, planed, thickness of 20 mm. These were then trapeze edged to be used in CLT panels. Only 20 mm thick panel layers were considered in this scenario.
In this scenario, all 2,214 logs with a top diameter of less than 185 mm were live sawn, using four different sawing patterns defined. The boards were sawn at 24, 35, or 46.5 mm green thickness, which corresponded to a nominal, planed, thickness of 20, 30, and 40 mm, respectively. All produced flitches were used for CLT production, and the panel thicknesses were 20, 30, and 40 mm.
For both CLT scenario A and B, the yield was calculated as the total volume of CLT panel layers divided by the total volume of the logs. The sources of material losses incurred from log to CLT panel layer were: Sawing, drying, planing, edging, crosscutting, and finger-jointing.
In Scenario A the yield is decreased by 0.9 percent units compared to the reference scenario. For scenario B, there is an increase of 17.4 percent units compared to the reference. The results presented in this paper show that compared to cant sawing and straight edging, live sawing combined with trapeze edging can increase the yield for logs with top diameter of less than 185 mm. When using logs with a top diameter of up to 400 mm, and using the sideboards in a cant sawing pattern for trapeze edging and CLT production, the yield is decreased compared to cant sawing and straight edging of regular sawn timber.
The reason for this is probably that larger logs mean higher yield using cant sawing patterns and straight edging compared to small diameter logs, so the positive effects of the edging method are mitigated by the CLT production operations that decrease yield, compared to just sawing, drying, and planing regular boards.
It can also be speculated that a trapeze edging method would result in lower usage of glue than using straight, fingerjointed boards, both due to the absence of fingerjoints and due to the larger average width of the trapeze edged pieces compared to straight edged pieces. This would result in both lower material costs in production as well as a more environmentally friendly product.
This study was made on a rather specific production scenario, and the results should be interpreted in the light of this fact. However, the large amount of logs used and the large volume yield increase for small diameter logs suggest that there is a positive potential in using a method such as this, to process small diameter logs in a more material efficient way.
To realize a trapeze edging method in practice would require separate handling of small diameter logs in a sawmill, or a sawmill specialized in sawing small diameter logs. Edging machinery would need to be adapted to facilitate trapeze edging. Also needed is a specialised production line for making CLT out of trapeze edged pieces, with equipment for scanning and turning the pieces in the correct way to keep layers as straight as possible.
Otherwise, since CLT layers for wall panels usually are rather long, there is a risk of curved panels. This study did not take into account that different amounts of panels or different panel thicknesses will be needed in a real production process, which will affect the yield and choice of sawing patterns etc. The edging algorithm is possible to implement using a numerically controlled edging machine, since the mathematical and programmatic methods used are rather straightforward.
The method would depend on purpose built hardware in terms of sawing machines though. There will be increased handling and surveillance operations associated with the proposed method compared to traditional CLT production, which affect profitability. This was not accounted for in this study. Also, an increased volume yield would mean less material such as sawdust and wood chips available for energy or pulp production.
It is probably more profitable to use the wood material for a relatively high valued CLT product than for a relatively low valued product such as sawdust. It is necessary to take this into account when assessing the profitability of the method however. Overall, the results are an indication that the potential for a trapeze edging method is very high when it comes to utilizing small diameter logs in a material efficient way.