A common problem in outdoor wood flooring is the risk of accidents due to slipping. Skid resistance is the property of a surface to provide a pedestrian with a safe grip. It depends on the surface material, and design, the shoe sole worn by the pedestrian and the condition of the surface (dry or wet).
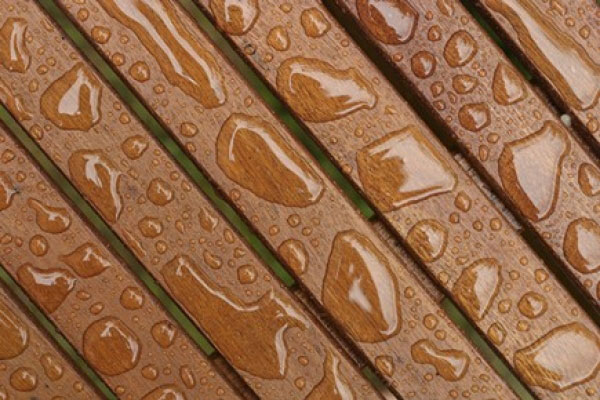
Skid resistance is determined using a portable skid resistance meter, which consists of a pendulum with a rubber-coated foot piece which oscillates on the sample to test. The pendulum is stopped by the friction between the rubber and the sample. The maximum oscillation is indicated on a scale from 0 to 150 (there are no units involved) with a high value indicating high anti-skid resistance.
A combination of chemical (solar degradation, lixiviation and temperature), biological (fungi and mosses) and mechanical processes (flooring wear due to traffic) develop a set of reactions that finally contribute to the surface degradation, which is followed by the increasing risk of skid and probable falls.
The Spanish Construction Regulations (CTE-DB-SU) requires that the skid resistance of outdoor flooring must be higher than 45. A common method to increase the outdoor performance of wood floorings is the application of anti-skid resistance coatings. The selected wood species should prove to be effective during the service life of the flooring.
Porosity Of Wood
High density woods have a lower void space (pores) between wood elements, which has an effect on the absorption of the coating. The amount of pores varies greatly depending on the species. Furthermore, their size, shape and frequency are determined by the cut of the exposed surface (tangential and radial). Commonly, coniferous wood is more porous than the wood of deciduous species. In addition, the pores of coniferous wood are more uniformly distributed.
Moisture content is a critical factor to consider, since wood is a hygroscopic material. Water fills the void space in wood, resulting in a physical obstacle for the absorption of the coating. Furthermore, high moisture content prevents the cross linking of polymers and produces defective drying which causes a lack of adherence of the coating.
For appropriate application and correct subsequent coating drying, the amount of moisture should not exceed 20 percent. Therefore, it is important to consider the fibre saturation point (FSP), namely the moisture content at which the cell wall is saturated with moisture. This property varies greatly between species, and normally is lower in species with a high content of extractives.
The presence of extractives in wood affects the absorption of the coatings and its curing on the surface of the wood. During the drying of wood the extractives are transported to the surface in a heterogeneous distribution, causing their concentration in certain parts of the boards. In addition, heated wood releases exudates that interfere with absorption, curing, and anchorage of coatings. Conifer woods are rich in resinous substances, whereas deciduous wood are richer in tannins.
Furthermore a radial cut has greater dimensional stability compared with a tangential cut. Therefore, a radial cut results in a better coating finish than a tangential cut. This fact shows the advantages of using wood species with a low coefficient of volumetric contraction.
Wood finishes and their final behaviour can be described as a three component system: wood, coating and the relations coatings-wood. The final result not only depends on the anatomical properties of each species, but also the characteristics of the different coatings.
Penetration Of Coating
An important parameter in the performance of coatings is the capability to penetrate the wood structure. Several methods have been applied and tested to investigate the penetrating ability of coatings in wood, and the different cellular distribution of it by techniques of X-ray analysis and means of florescence microscopy. Penetration of coating into wood is first of all determined by the ability of the paint to flow into the open ends of the cell capillaries.
Differences in penetration depth are influenced by the paint system, the type of binder, particle size of the binder, and type of solvent. Generally the waterborne coatings penetrate less deeply into the wood structure than the solvent-borne coatings, although large differences between water-borne coatings exist, depending on the type of formulation used.
In addition, previous studies have concluded that the type of binder has the biggest effect on wood penetration, with the following increasing order in penetration: acrylic dispersion, alkyd emulsions, solvent borne alkyds and high solid alkyds.
Moreover, in relation with the different cellular distribution of coatings within the structure of the wood, the axial penetration is deepest in the solvent based coatings, and in the water borne the penetration is deepest in the wider earlywood cells, whereas for the solvent borne coatings the situations is reverse. This might indicate that the basic flow mechanisms are different in water and solvent based coatings.
The combination of viscosity, surface tension, drying rate of the coating and the diameter of the wood pores determine the penetrating capacity of coating. With lower viscosity and lower surface tension the penetration becomes deeper.
In order to evaluate the effect of species in the performance of six different outdoor coatings with anti-skid properties, 154 samples of chestnut wood and 154 of pine wood were used in the experiment. Five different coatings offered in the Spanish market were chosen according to the following criteria: anti-skid abilities, colour, ease of application and price.
The dimensions of the samples were 70 x 85 x 85 cubic mm and 10 x 100 x 100 cubic mm for the skid resistance test and film thickness, respectively. The coatings were applied on glass to observe the presence of minerals and the texture with a stereoscopic magnifying glass with a zoom ratio of 6.3:1.
The presence of mineral particles was determined using a plastic square mesh with apertures of 1.90 x 2.35 mm by counting the number of squares in the mesh that contained mineral particles and dividing it by the total mesh area. Before applying the coatings to the wood, the samples were sanded with half grain N 100 to 120 paper. Two coats of finish were applied by brush according to the manufactures instructions. The plane of section of the samples (tangential or radial) was noted.
The coating retention level was calculated as the ratio between the difference in dry mass of the sample before and after application of the coating divided by the area of the samples. The mass was determined with a balance. Film thickness was measured using ultrasonic equipment following the standard UNE-EN ISO 2808. The result was taken as the average of three measurements.
The determination of the skid resistance was carried out according to according to UNE-ENV 12633 standards, using a friction pendulum. The samples (10 repetitions per coating) were immersed in water at 20±2 deg C for 30 minutes and then were sprayed with water on the contact surface.
The test sample was fixed firmly with its longest dimension in the same direction as the swinging of the pendulum, and centred with respect to the rubber flange and the axis of suspension of the pendulum. The skid resistance value for each coating and species was taken as the average value of the pendulum obtained for the 10 samples tested.
The statistical analysis included the test of the distribution of all variables checked was tested using the Shapiro-Wilk test and the effect of treatments on the dependent variables was checked using the Kruskal-Wallis non-parametric test. Once the effect of the treatments was verified, a multiple comparison was performed between medians using the Wilcox test.
Coating Retention Level
It was observed that gamma and mu had a coarser texture (larger particles) with a higher presence of mineral particles, 97 and 85 percent respectively, followed by theta with minerals present in 81 percent of the total area. Beta showed a low presence of minerals, 22 percent, but a porous texture different to the other coatings studied. Finally, the open pore finish Lambda presented a silky texture and a very low presence of mineral particles, six percent.
The coating retention level did not have a normal distribution. All coatings studied showed a significant effect on the coating retention level. Additionally, all coatings presented significant differences between chestnut and pine, except open pore finish lambda. With the exception of the coating mu, all coatings showed higher coating retention level in pine than in chestnut.
According to the type of solvent, the highest coating retention level was found for gamma, mu and theta. These coatings have an organic solvent, and in agreement with qualitative descriptions of coating penetration showed in a previous study, the organic solvent coatings has a deeper penetration than aqueous solvent.
The film thickness did not present a normal distribution. Coatings beta, gamma and lambda had a significant effect, depending on the species, on the film thickness. As was observed for coating retention level, the thickness of all coatings was higher in pine than in chestnut.
The differences in coating retention level and film thickness observed in the two species can be attributed to the fact that pine has a lower density than chestnut and therefore a greater volume of voids.
Consequently, a higher absorption of liquid can be expected. In addition, pine is of finer texture than chestnut, and with a medium grain, allowing for better preparation of the surface prior to the application of the coating.
There was no significant difference between the results of the two planes. The absorption coefficient for the chestnut was lower than that of the pine. Even though the coatings had an organic solvent base, the water absorption coefficient can be considered an indication of the mechanisms for liquid absorption which could explain the differences between chestnut and pine.
The determination of the skid resistance showed that, for both species, the coatings gamma and mu were more resistant to skid, followed by beta. The open pore finish Lambda, which used as a reference, presented the lowest anti-skid resistance for the chestnut and one of worst for the pine.
Additionally, the effect of the plane of section on the skid resistance demonstrated no significant differences. Consistently pine as a substrate presented higher values of skid resistance, coating retention level and thickness. The lower performance of chestnut can be attributed to the high content of extractives, which are reported to hinder the anchorage and curing of coatings. Furthermore, pine has a higher water coefficient of absorption.
A plausible hypothesis to explain the difference between species is that in pine the liquid component of the coating is absorbed, leaving the mineral particles exposed on the surface. Therefore, the grip function of the coating is accomplished more successfully. On the contrary, chestnut absorbs the liquid coating poorly, and the mineral particles remain within the film.
Additionally, gamma and mu had a coarser texture, with a higher concentration of mineral particles. Both coatings showed the best skid resistance, irrespective of the species. The open pore finish lambda showed the worst results for skid resistance, confirming that the anti-skid function of coating is important to accomplish a finishing that complies with the construction regulations.
Independently of the coating tested, pine presented a higher skid resistance than chestnut. Additionally, for each coating tested thickness and coating retention level were significantly higher in pine than in chestnut, showing a better development of the film. For both species, mu and gamma demonstrated a coarsest texture, a higher concentration of mineral particles and the higher anti-skid resistance.
Overall, pine has a better coating performance than chestnut. Nevertheless, chestnut performs acceptably if the adequate coating system is used. Finally, the results show the importance of designing the coating according to the wood species, since wood is not an inert substrate and could seriously affect the performance of the coating.