In the recent years, the interest in indoor air quality has increased considerably. The presence of some substances in indoor air may cause many health problems, such as diseases of the respiratory tract, allergies, migraines and overall irritation. Many researchers are of an opinion that these health problems are caused by volatile organic compounds. Volatile organic compounds (VOCs) are emitted from many sources, both internal and external.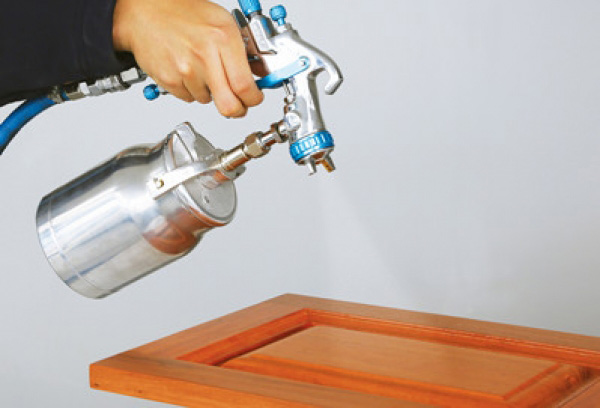
Increasing interest in indoor air quality in housing buildings, office buildings, schools and hospitals has resulted in the subject being discussed in relation to industrial practice. There are limited studies on VOC emissions and air pollution in industrial practice, including the different sectors of the wood industry. Studies performed on the wood industry mainly discussed VOC emissions from wood, lacquer coatings and finished products. Such pollution occurs first of all during the process of lacquering of furniture elements.
For this reason, a study was conducted with the aim of determining the effect of application methods of lacquer products used in the furniture industry on the microclimate of facilities, in which the finishing operations were performed on surfaces of furniture items.
In order to determine the effect of lacquer product application methods on the emission of volatile organic compounds, investigations were conducted in three furniture manufacturing plants producing case furniture. Production in these plants is based on modern technological solutions, both in rough wood processing and secondary processing as well as surface finishing.
Effects Of Application Methods
All the plants selected for the study in the finishing process use only lacquer systems based on waterborne binders, which were applied on the surface of furniture elements using different lacquer application methods and machines.
In the plant 1, the process of furniture surface finishing was based on:
•An automated finishing line (1) for lacquer application and drying, consisting of a belt sanding machine, a dust suction device and an oscillating spray machine with the electronic control unit for panel dimensions reading, a belt conveyor and the lacquer recovery system and a drying tunnel, composed of the following segments: heating (to a temperature of 30–40 deg C), drying using IR radiators (at a temperature of 60 deg C) and conditioning to ambient temperature.
Incoming air by means of the air pressurisation unit moves overspray to the filtering system and is then carried to the exhaust fan. Suction system composed of a double set of dry filters.
•An automated vertical spray machine, equipped with two spray guns. The spraying was performed in a spraying booth.
The lacquering booth consisted of two rooms—a painting room of 4.9 x 3.9 m (L x W) and a drying room of 7.6 x 4.9 m (L x W). Pure air was supplied to the booth through the filter ceiling. The air filtration process consisted of preliminary and final filtration stages. Dusted air was discharged through a filtering water curtain.
In the plant 2, the furniture surface finishing process was performed using:
•An automated finishing line (2) for lacquer application and drying, equipped with a standing belt machine, a reading line with photocells to identify dimensions of processed elements, a drying tunnel with IRM lamps, an automated spray machine with six spray guns, a drying tunnel composed of the following zones: the drying zone using microwave electromagnetic radiation energy (the Microwaves Operating System—MOS), the drying zone with hot air injection in a nozzle tunnel with IRM lamps, the conditioning zone adjusting the temperature to ambient temperature.
Air purity in the lacquering chamber was provided by two fans coupled with filters. The unit is supplied with ambient air using an electric fan. Overspray is sucked in by two pipes mounted on an elevator using an exhaust fan and passes through the system of two filters: a prefilter and an after filter.
•Manual pneumatic guns in spray booths with dry filters. The lacquering unit was equipped with the supply- exhaust ventilation system. The ventilation system was equipped with two filters: a cardboard pleated filter and a Paint-Stop filter mat.
Plant 3 was equipped with:
•A 1-headed curtain coater. The curtain coater was located in the hall equipped with a mechanical supply-exhaust ventilation system, meeting requirements of the current technical and legal requirements concerning the operation of the plant. It was confirmed by the positive results of environmental analyses conducted at the plant on a regular basis. The lacquering stand was not equipped with a local exhaust ventilation.
•Lacquer application booths with dry filters with manual pneumatic guns. Spray booths were equipped with the supply-exhaust ventilation system. Contaminated air was purified in a single stage process: using a cardboard pleated filter.
The air for analyses was collected to glass tubes filled with a Tenax TA solid sorbent at 120 mg (35/60 mesh). Each time, five parallel air samples were collected using a pump (FLEC Air Pump 1001). The analyses were performed at the lacquer application zone at a distance of approximately 0.5 m from the lacquer application machines. The samples were collected at a height of 1.5 m above floor level. The volume of 500 ml air was transferred by the sorbent at a rate of 50 ml/min.
The volatile organic compounds adsorbed on the Tenax TA were released in a thermal desorber and next, they were determined by gas chromatography combined with mass spectrometry.
The compounds were identified by comparing the recorded mass spectra with the spectra contained in the NIST MS Search library and confirmed by referring the mass spectra and retention times of identified compounds to the spectra and retention times of appropriate standards. Quantitative analysis of volatile organic compounds emitted from investigated surfaces was conducted by adding a reference standard 1-bromo-4-fluorobenzene.
Air Quality
In the plant 1 equipped with a modern finishing line (1)and an automated vertical spray machine, the concentration of all volatile organic compounds at the lacquer application zone was in a very broad range of values from 2287 μg/cubic metre to 9398 μg/cubic metre. In the air, collected from the lacquer application zone on the finishing line (1) the detected compounds included particularly toluene, 1-butanol and 2-butoxyethanol at 768.6 μg/cubic metre, 721.1 μg/cubic metre and 293.9 μg/cubic metre. Moreover, the presence of the following compounds was also detected: n-butyl acetate, hexanal and terpenes, mainly α-pinene and 3-carene.
In the course of lacquer application on furniture elements using an automated vertical spray machine, a broader spectrum of compounds was noted than that recorded at the application by the finishing line (1). When using the automated vertical spray machine, 2-butoxy-ethanol in the greatest amounts.
Concentration of the compound amounted to 4737.1 μg/cubic metre—almost 50 percent total concentration of all compounds found in the analysed air. High emissions were also recorded for 1-butanol (2075.8 μg/cubic metre), toluene (547.3 μg/cubic metre) and butyl acetate (501.0 μg/cubic metre).
Large differences in the total amount of all compounds released into the air are primarily the result of the increased concentration of 2-butoxyethanol and 1-butanol in the spray booth. Glycol concentration in the lacquer application zone, when automated vertical spraying was used, was over 16-times higher and that of alcohol was almost three-fold higher than at the lacquer application zone on the finishing line.
The concentration of the volatile organic compounds at the finishing line (2) amounted on an average to 3741 μg/cubic metre and it was lower than when applying coatings with manual spray guns in the lacquer application booth, equipped with dry filters, where it amounted to 4559 μg/cubic metre. In the tested air collected near the lacquer application zone on the finishing line (2) considerable amounts were detected for 2-butoxyethanol at 1264.9 μg/cubic metre, toluene at 401.7 μg/cubic metre, acetone at 299.0 μg/cubic metre, 1-butanol at 226,3 μg/cubic metre and hexanal at 231.6 μg/cubic metre.
The abovementioned compounds jointly accounted for over 64 percent of the total emission. The other substances emitted in smaller amounts included pentanal, butyl acetate, ethylbenzene, m,p-xylene, as well as terpene compounds.
It needs to be stressed that in the air collected at the finishing line (2) the presence of styrene was detected at 170.10 μg/cubic metre. Lacquer application on furniture surface in the finishing line (2) additionally caused by the emission of such compounds as acetone, pentanal, tetrachloroethylene and 1-butoxy- 2-propanol, whose presence was not detected in the air collected from the spray booth (2).
Risk Of Manual Application
In the air samples collected from a spray booth, in which manual spraying was applied, a smaller spectrumof compounds was detected than in the case of the finishing line (2). 2-butoxyethanol was the compound released in the greatest amount, at a concentration of970.5 μg/ cubic metre.
Lacquer application by manual pneumatic guns caused the emission of large amounts of 1-butanol(944.5 μg/cubic metre) and butyl acetate (700.1 μg/cubic metre).Emissions of 2-butoxyethanol, 1-butanol and butylacetate accounted for over 80 percent of all the released compounds.The measurements taken in the plant 3 made it possible to compare the technology of surface finishing using curtain coater with manual spray pneumatic guns.
They showed that lower air pollution is caused by manual spray guns in a lacquer application booth than by a curtain coater. The concentration of volatile organic compounds near the lacquer application zone in the curtain coater was 7606 μg/cubic metre, while at the lacquer application workstation with the use of manual pneumatic guns it was lower amounting on an average to 5911 μg/cubic metre.
In the plant 3, where the undercoating product was applied, a spectrum of compounds was found similar to those detected in the two other plants. The compound released in the greatest amount turned out to be 2-butoxyethanol.
Finishing of furniture elements by curtain coating caused emission of this compound at 2829.6 μg/cubic metre, while lacquer application with the use of manual guns resulted in emission at 2207.3 μg/cubic metre. In the tested air, high concentrations were also detected for acetone, 1-butanol, toluene and 1-butoxy-2-propanol. Lower amounts were recorded for pentanal, n-butyl acetate, hexanal, m,p-xylene as well as terpenes, 3-carene and limonene.
Tested air samples collected from the furniture element lacquer application zones contained such compounds as aldehydes, ketones, aromatic hydrocarbons, alcohols, glycols and terpenes. Sources of their emissions included both finished furniture elements and applied lacquer systems. Wood species were sources of emissions of aldehydes, pentanal and hexanal.
These compounds are formed through oxidation reactions of unsaturated fatty acids found in wood. Pentanal is formed as a result of oxidation of linoleic acid, while pentanal is the product of oxidation of linolenic acid. Terpene compounds (α-pinene, 3-carene, limonene) are also emitted by various wood species, particularly softwood. Acetone is a compound detected during analyses of emissions of volatile organic compounds from different wood species, wood-based materials and lacquer systems.
Presence Of Styrene
It is rather difficult to explain the presence of styrene in air collected from the lacquer application zone at lacquering line 2. Available literature contains practically no information on emission of styrene from aqueous systems. Moreover, this compound was not detected during the application using spray guns.
Emission of styrene is possible from waterborne products cured using UV irradiation. Styrene is used for copolymerisation of UPE-systems. A study has showed that UV-cured aqueous products based on unsaturated polyester (UPE) may be sources of styrene emission. In the analysed lacquering line (2) both aqueous products and UV-cured aqueous products may be applied alternately.
It may be assumed that styrene detected in the lacquer application zone at lacquering line (2) did not originate from the analysed systems, but rather from the UV-cured aqueous products applied earlier at the same line.
On the basis of the conducted tests, it was found that in the analysed plants emissions of volatile organic compounds varied and to a considerable extent depended on the type of the used lacquer application machine or device.
The highest TVOC content was detected in the air collected from the lacquer application zone with automated spraying amounting to 9398 μg/cubic metre, while the level for the use of a curtain coater was 7606 μg/cubic metre.
Automated finishing lines proved to be superior in comparison to the other machines. Concentration of VOCs was 2287 and 3741μg/cubic metre. In the case of manual spraying, the level of emission from the lacquer application zone was varied ranging from 4559 5911 μg/cubic metre to 5911 μg/cubic metre.
When comparing technologies of lacquer product application, in which identical lacquer products were applied, it needs to be stated that VOCs emissions in the plant 1 were four-fold higher when using automated spraying than in the case of surface finishing of furniture on the finishing line.
In turn, in the plants 2 and 3 these differences were less marked. The finishing line installed in the plant 2 in the lacquer application zone caused air pollution with volatile compounds by 20 percent higher than the lacquer application with the use of manual pneumatic guns. In turn, in the plant 3, surface finishing with the use of a curtain coater contributed to VOC air .(fdmasia)